12 Factors That Influence Freight Shipping Costs
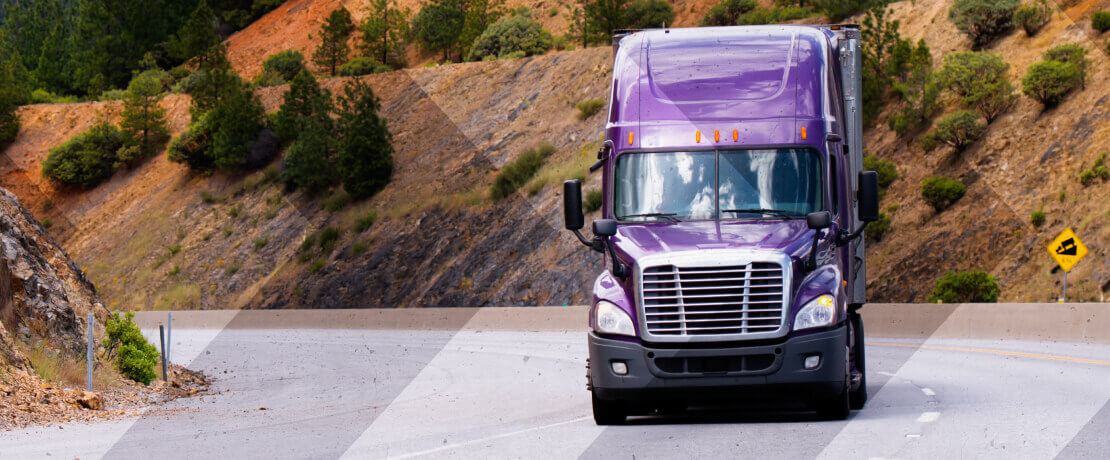
Make data-driven decisions.
Grow your business with competitive pricing and negotiating.
Shipping is a multi-layered industry with a lot of variables to take into account. Here are 12 things that affect shipping costs and what they mean to you.
In an industry so large, you might think there would be a freight shipping cost standard. But there isn’t one. Because freight shipping costs depend on so many factors, getting an accurate freight shipping estimate is surprisingly complicated.
Part of it is the regional nature of shipping. Some carriers serve specific regions or shipping lanes better than others and can manage a smaller area meticulously. But shipping costs can vary for many reasons and can end up being quite different from the broker’s original freight quote. Freight rates might also differ from carrier to carrier, so multiple quotes may show different costs.
1. Dimensions and weight
When shipping a truckload (or trailer full) of goods, you’re usually charged a per-mile rate — called a per-hundred weight charge — plus fuel costs. This is a pretty simple calculation. But in the case of “less than truckload” (LTL) shipping, the freight dimensions and weight determine the cost. Weight rates are structured so that the heavier your load, the less you pay per 100 pounds (“per hundred-weight”).
Dimensions are measured in cubic feet. The freight’s cubic feet and weight help determine the next factor in shipping cost: freight density.
2. Freight type
The type of freight being shipped and the type of trailer required also impact rates, such as:
- Dry van freight: Most shipments in the U.S. are dry van shipping trailers, which are not temperature controlled.
- Reefer freight: Refrigerated freight uses temperature-controlled trailers that hear or cool the goods to keep them at the proper temperature.
- Flatbed freight: Flatbed trailers are used for large or bulky cargo, items that do not fit inside a dry van, and goods that do not need protection from the weather, such as lumber or machinery.
3. Freight density
To determine freight costs, you also need to know your freight density. Calculate freight density by dividing the total weight of your shipment by the total cubic feet. For shipments on a pallet, use the dimensions of the pallet. Be sure to include the pallet weight in the overall shipment weight. Always measure the longest side, including any overhangs beyond the pallet.
4. Freight class
Freight class is more complicated. Each freight piece falls into one of 18 classes established by the National Motor Traffic Association in the National Motor Freight Classification book. The lower the class, the less expensive it is to ship.
- Several factors determine class, including:
- Product density
- Value
- Stow-ability
- Handling
- Liability
Lower class loads have higher density, are easier to handle, and are the least susceptible to damage. Lighter, more fragile loads fall into a higher class and cost more to ship; this freight tends to take up more room and is harder to handle.
5. Distance freight is shipped
How much does freight shipping cost from state to state? Well, the greater distance the freight has to go, the higher the cost. Regional carriers typically serve a particular area. If goods are shipped outside that area, the regional carrier will have to transfer them to another carrier that delivers in that Zip code.
This practice, called interlining, often negates any discounts you might get for shipping within specific areas. Other costs are usually involved, too.
6. Destination type
The more conditions your shipment has to the final destination, the greater the freight cost. Drivers also factor in the cost of time spent at a delivery site. The harder it is to deliver with a fast turnaround, the more your shipping will cost you.
Here are some other locations with potential conditions that could impact your shipping costs:
- Storage units
- Churches
- Schools
- Commercial establishments not open to the public (with a guardhouse and fencing, for example)
- Military installations
- Construction sites
- Farms
- Fairs or carnivals
7. Shipping mode
Shipping mode refers to how fast you need your shipment to arrive. You can choose expedited shipping for urgent timeframes, but it’s more expensive. Consolidated freight shipping with a more flexible time window saves you money, but might be out of your control if your customer needs the goods by a specific time. However, if you can plan shipments, you’re more likely to get the best rates available.
Freight shipping rates will also vary depending on how the freight is being shipped:
Full truckload (FTL): FTL uses the entire space within your hauler.
- Partial truckload (PTL): A partial truckload doesn’t fill the entire trailer, allowing carriers to take multiple loads and maximize earnings per trip. Loads typically stay on the truck and are delivered to a common location.
- Less than truckload (LTL): LTL freight is similar to PTL in that multiple loads may be combined. With LTL, however, freight may need additional handling, make multiple stops, or be offloaded separately.
- Intermodal: Intermodal freight combines multiple shipping methods, such as loads transported by road and rail.
8. Fuel costs
Shipping rates go up when fuel costs, especially diesel, are higher in a specific area due to taxes, market forces, or other regional factors. When fuel prices drop, shipping costs should go down accordingly. If fuel prices are volatile at the time you’re shipping, carriers might set their rates higher to protect themselves against sudden fuel price hikes.
Keep in mind that state-to-state shipping is often more expensive due to fuel costs as well. State fuel rates vary broadly based on local and state taxes. The fuel costs in your area may not be the same as fuel costs in the shipment area. Some truckers use fuel surcharge calculators to estimate these costs, which are generally factored into shipping costs.
9. Freight demand
The law of supply-and-demand applies to shipping as well. If space on trucks is limited, carriers may sell that space at a premium rate. But if shipping is slow, costs might dip lower as carriers try to fill trailers.
The shipping demand and the number of carriers in your area can dramatically affect your shipping costs, which might also vary from company to company. It’s always wise to shop around whenever possible.
10. Deadhead miles
Carriers don’t like partial loads or, worse, deadhead miles — driving with an empty trailer. The added cost of deadhead miles often comes up in rural areas. If you have to drive an empty trailer a long way to the next destination, that’s lost revenue.
11. Carrier minimums
All carriers have minimum rates. If a shipment falls below that minimum, you’ll be charged the minimum anyway, no matter how small your shipment is. For the most part, you should ensure that you have a shipment above the minimum before contracting a shipper or explore alternate shipping methods like FedEx and UPS.
12. Accessorial charges
If your shipment requires things like lift gates, inside delivery, residential delivery, or poses other access challenges for drivers, account for those challenges into your freight shipping rates. Commercial shipping is designed ideally for dock-to-dock shipping. Any variation from that will result in you being charged for the inconvenience. Accessorial charges can be anything from delivery to a strip mall to call-ahead appointments. Make sure you know all of those possibilities up front and factor them into the cost of each job.
Get the best rates every time.

If it feels like there are a lot of factors to consider, you’re right! How do you get the best rates every time? One way is to use the Truckstop Rate Analysis Tool. It uses rate data from across our platform that includes thousands of similar loads and more than one million power units.
Topics:
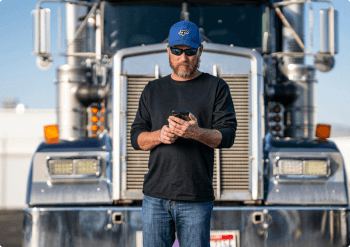
Find out how our platform gives you the visibility you need to get more done.
Get helpful content delivered to your inbox.
Schedule a demo.
Find out how our platform gives you the visibility you need to get more done.
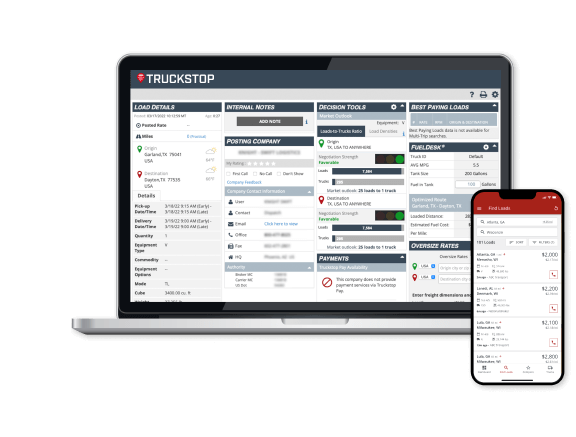